Did you know the type of injection molding machine you pick can greatly affect your plastic production’s efficiency and cost? With many THY Precision injection molding machine types out there, it’s key to know their special features and abilities. This knowledge helps you make a choice that fits your production needs well.
Key Takeaways
- Injection molding machines vary, each with its own power source and unique traits.
- It’s vital to understand the differences between hydraulic, all-electric, and hybrid injection molding machine types. This helps pick the most efficient one.
- Specialized injection molding machine types, like vertical and multi-component machines, are made for specific production needs.
- When choosing injection molding machine types, think about energy efficiency, production speed, and flexibility.
- Talking to experts can help you pick the best injection molding machine types for your business.
This guide will cover the various injection molding machine types and their special traits. It aims to help you find the most efficient and cost-effective solution for your plastic production. Get ready to boost your manufacturing process by finding the best injection molding machine types for your business.
Introduction to IInjection Molding Machine Types
Injection molding has changed how many industries make parts and components. At the center are machines that turn plastic into detailed, precise products. These injection molding machine types are key to making manufacturing faster, cheaper, and more efficient.
The Injection Molding Process
The injection molding process turns raw plastic into finished parts in steps. First, the plastic is heated until it’s molten. Then, it’s pushed into a mold at high pressure.
As it cools, the plastic takes the shape of the mold. This makes a product that’s the same every time. The machine’s Injection Unit and Clamping Unit work together to ensure quality.
Step | Description |
---|---|
Feeding | The raw thermoplastic material, typically in the form of pellets or granules, is fed into the injection molding machine’s hopper. |
Melting | The material is heated and melted within the barrel of the Injection Unit, transforming it into a viscous, moldable liquid. |
Injection | The molten material is then forced, under high pressure, into the closed mold cavity, taking the shape of the desired part. |
Cooling | The material cools and solidifies within the mold, retaining the shape of the part. |
Ejection | The finished part is then ejected from the mold, completing the injection molding process. |
The injection molding process is great for making lots of the same part quickly and cheaply. It’s used in many industries, like cars and electronics. Knowing how it works and the different injection molding machine types helps manufacturers improve their production.
Types of Injection Molding Machine Types Based on Power Source
The power source is key in choosing the right injectionmoldingmachine. In the U.S., hydraulic injection molding machines are a top pick for many manufacturers.
Hydraulic Injection Molding Machines
Hydraulic injectionmoldingmachines started in the late 1800s. They use hydraulic pressure to close the mold and fill it with melted plastic.
These machines are loved for their long life and cost-effectiveness. They’re also easy to fix and maintain. Plus, they can handle big molds with ease, thanks to their strong clamping forces.
Feature | Hydraulic Injection Molding Machines |
---|---|
Power Source | Hydraulic |
Clamping Force | 3-4 tons per square inch |
Suitability | Large mold production |
Advantages | Affordable, rugged, easy to source and repair |
Hydraulic injectionmoldingmachines are still a favorite in the U.S. They offer a dependable and budget-friendly way to meet injection molding needs.
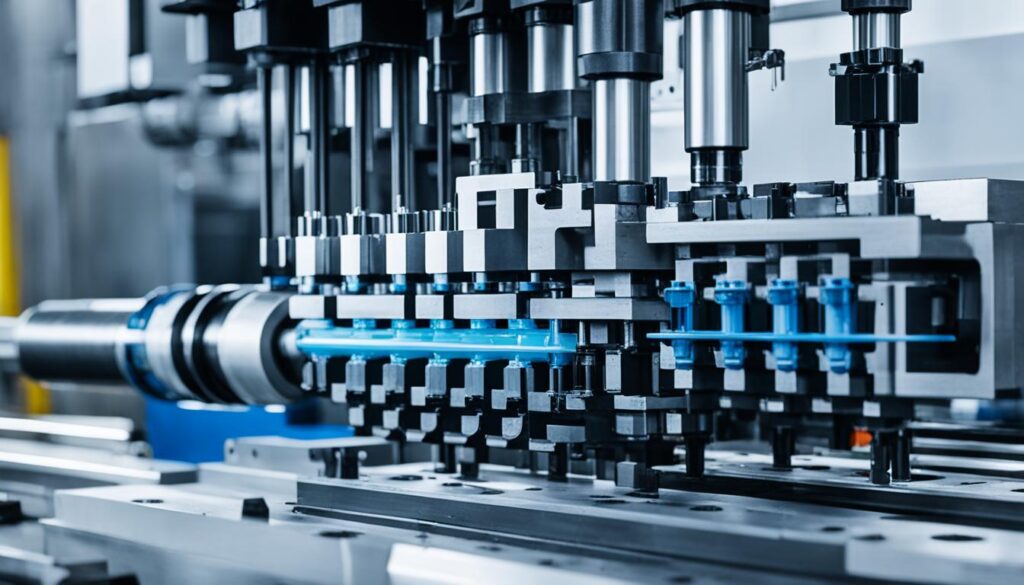
Energy Efficiency in Injection Molding Machine Types
Energy efficiency is key when looking at injection molding machine types. THY Precision leads in making injection molding machines that save energy. They’ve introduced all-electric machines for this purpose.
These injection molding machine types are a new take on older machines. They use digital motors for better control over the molding process. This means they can save up to 75% more energy than old hydraulic machines.
Another great option is the hydraulic-electric hybrid machine. It combines the best of both worlds for a powerful and efficient process. This is perfect for businesses wanting to save on energy and improve their operations.
Injection Molding Machine Type | Energy Efficiency |
---|---|
Electrical (All-Electric) | Up to 75% energy savings compared to hydraulic models |
Hydraulic-Electric Hybrid | Highly effective, precise, and energy-saving |
THY Precision is leading the way with these injection molding machine types. Their machines are not just good for the planet. They also help businesses save money and run more efficiently over time.
Specialized Injection Molding Machine Types
Vertical injection molding machines are a special type of injection molding machine. They are great for making big, heavy, or long parts. This makes them perfect for making things like household appliances, car parts, and industrial items.
These machines are also great because they don’t take up much space. They are perfect for factories that are short on space. Plus, they can handle more pressure, which lets them make complex parts.
Vertical Injection Molding Machines
Vertical injection molding machines work differently from horizontal ones. They are easier to use, keep up, and improve. This is why they are a top pick for companies that need flexibility and efficiency.
THY Precision is a top name in injection molding machines. They offer a wide range of vertical machines that meet many industry needs. Their machines are designed to boost productivity and efficiency.
Feature | Vertical Injection Molding Machines | Horizontal Injection Molding Machines |
---|---|---|
Floor Space | Smaller footprint | Larger footprint |
Clamping Force | Higher clamping force | Lower clamping force |
Part Size | Suitable for larger, heavier, or longer parts | Better suited for smaller parts |
Applications | Household appliances, automotive components, industrial products | Wide range of applications, including consumer goods |
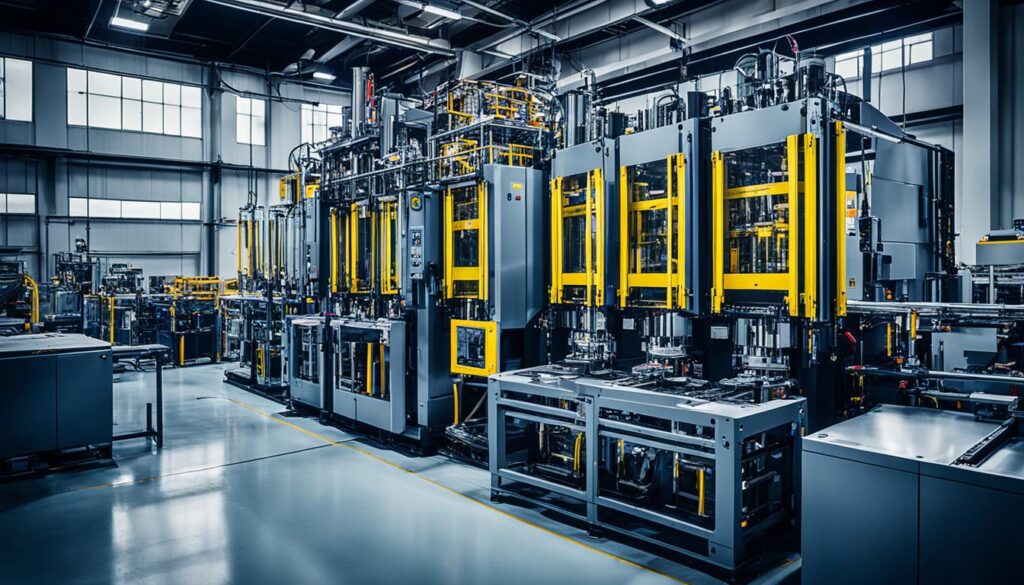
The need for specialized machines like vertical injection molding machines is growing. Companies want to improve their production and meet new market needs. They are looking at innovative solutions from companies like THY Precision.
Factors to Consider When Selecting injection molding machine types
When picking an injectionmoldingmachine, think about a few key things. The size and complexity of the parts you’re making, the clamping force needed, and the material type are all important. These elements greatly affect your choice.
Think about how much you plan to produce and how fast you need to do it. Also, consider how energy-efficient and sustainable the machine is. These can greatly affect your costs over time.
Don’t forget to look at the precision you need, if you want special features like in-mold labeling, and the space you have. These factors will help you pick the right machine for your business.
Factor | Considerations |
---|---|
Part Size and Complexity | Evaluate the dimensions and intricacy of the parts you need to produce to ensure the machine can handle the job. |
Clamping Force | Determine the required clamping force to hold the mold in place during the injection process. |
Material Type | Consider the specific properties and requirements of the materials you’ll be using, such as melting temperature and viscosity. |
Production Volume and Speed | Evaluate your anticipated production needs and ensure the machine can keep up with the desired output. |
Energy Efficiency | Look for machines with energy-saving features to minimize your operating costs and environmental impact. |
Precision Requirements | Determine the level of accuracy and consistency needed for your parts, and choose a machine that can meet those specifications. |
Specialized Features | Consider whether you need additional capabilities like in-mold labeling or multi-component molding. |
Available Floor Space | Ensure the injectionmoldingmachine fits within the available space in your facility. |
By carefully evaluating these factors, you can select the best injectionmoldingmachine to meet your specific manufacturing needs and achieve optimal efficiency and productivity.
“Choosing the right injectionmoldingmachine is crucial for the success of your manufacturing operation. Taking the time to thoroughly consider all the relevant factors will help you make an informed decision that pays dividends in the long run.”
Conclusion
Exploring the world of injection molding machine types shows how important they are in making things. Each type, from hydraulic to electric and hybrid, has its own benefits. These benefits can help meet your production needs.
At THY Precision, we know picking the right injection molding machine types is key. It helps improve your operations, make better products, and grow sustainably. Think about the power source, energy use, and special uses to make a smart choice.
If you’re new or experienced in injection molding machine types, THY Precision can help. We offer the knowledge and support to help you use your production to its fullest. Start your journey to better efficiency, saving money, and innovation with the right injection molding machine types.